Chanllege
Sebastian is a project enginner in a Bicycle Accessories Parts Compay, they were looking to optimize their production process to increase efficiency and reduce costs. One of their major challenges was the processing of new design aluminum alloy parts, which required a complex and time-consuming machining process for them, and wants to bring his products to market as early as possible. However, there are some challenges they are facing:
1) Technical challenges:The new bicycle parts machining design may have required the company to invest in new machinery. This could have presented technical challenges such as compatibility issues, breakdowns, or the need for specialized training for employees to operate the new equipment.
2) Cost overruns:Implementing a new bicycle parts machining design can be costly, especially if it involves investing in new machinery or reconfiguring the production line. The company may have underestimated the costs involved, which could have led to budget overruns and financial constraints.
3) Quality control:Whenever a new bicycle parts machining design is introduced, it's important to ensure that the new cnc machining process does not compromise the quality of the finished product. The company may have faced challenges in maintaining quality control during the transition to the new bicycle parts machining design, which could have impacted customer satisfaction.
And then, Sebastian found us through his friend, the lead engineer in the automotive industry. He told us his troubles and then sent us his drawing, we had a meeting and showed him our CNC machined and test equipment. And the next day, our engineering team sent him the DFM file and some suggestions.
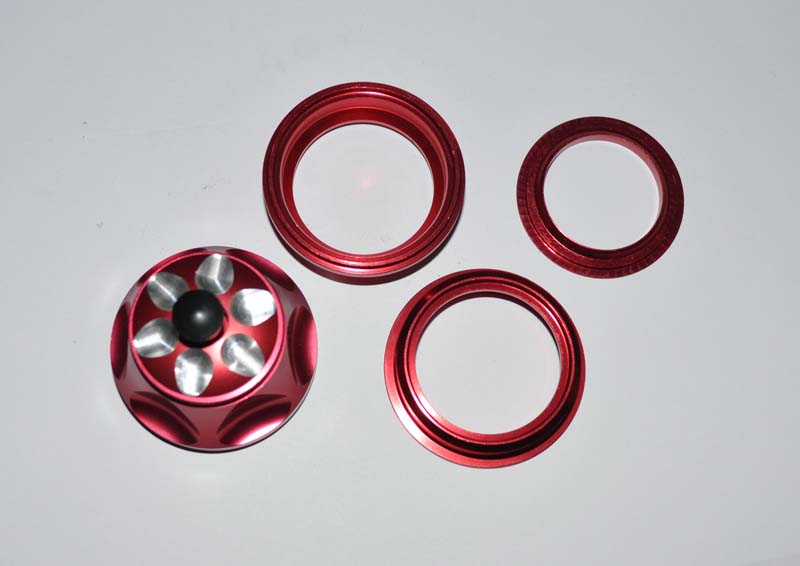
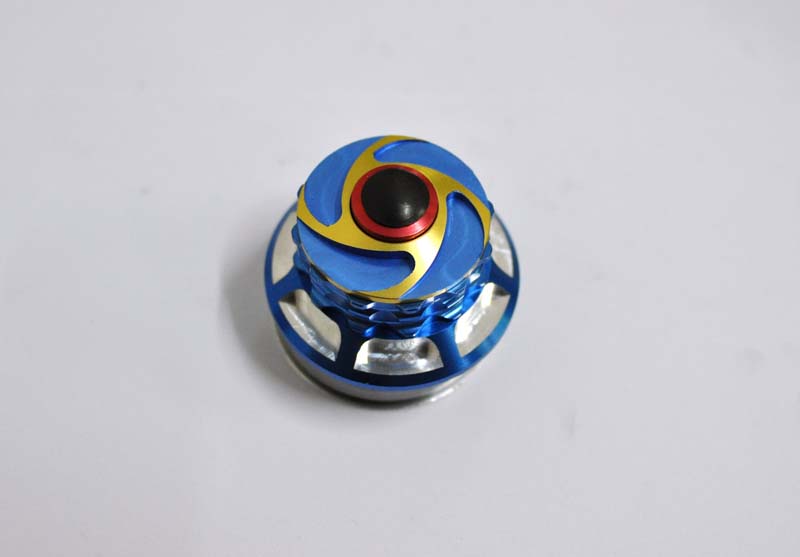
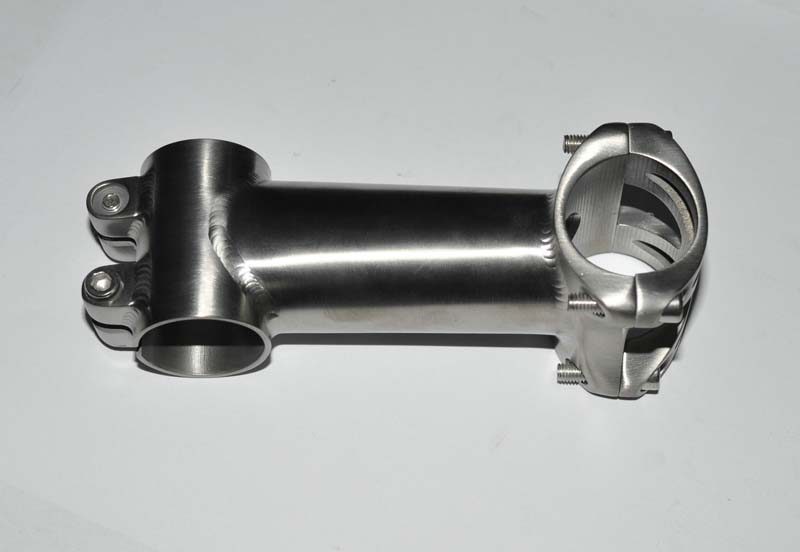
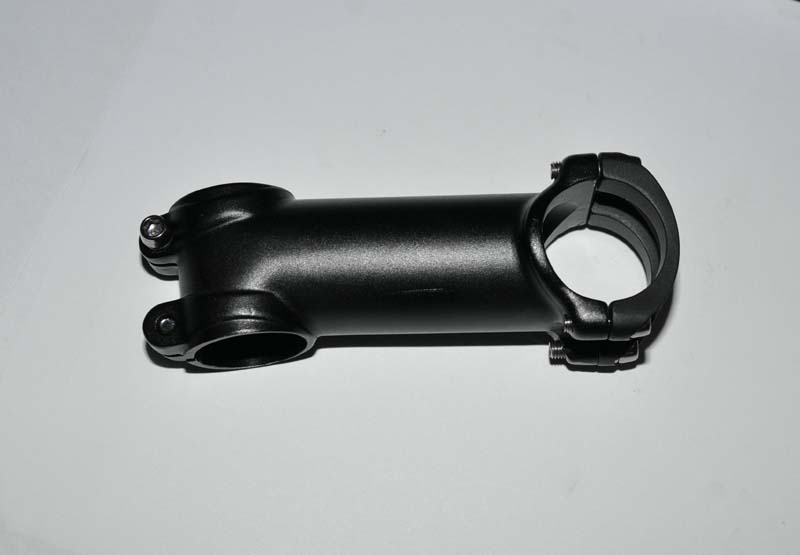
Make Professioal and Smooth DFM Analysis:
Design for manufacturing (DFM) analysis is an important step in the design process to ensure that the product can be manufactured efficiently and cost-effectively. When receiving the drawings about a pedal. Our engineering team sent Sebastian the DFM analysis the next day. The material should be strong, lightweight, and durable, aluminum alloy is a good choice for it, and at the same time, this material could also be easy to machine and readily available, reducing time and cost. Besides, the pedal design should avoid undercuts or difficult-to-machine features that require specialized tools or techniques. What’s more, the pedal design should consider the assembly process. To ensure that the parts should be designed to fit together easily and securely, with minimal manual labor required. The assembly process should be designed to be efficient and cost-effective.
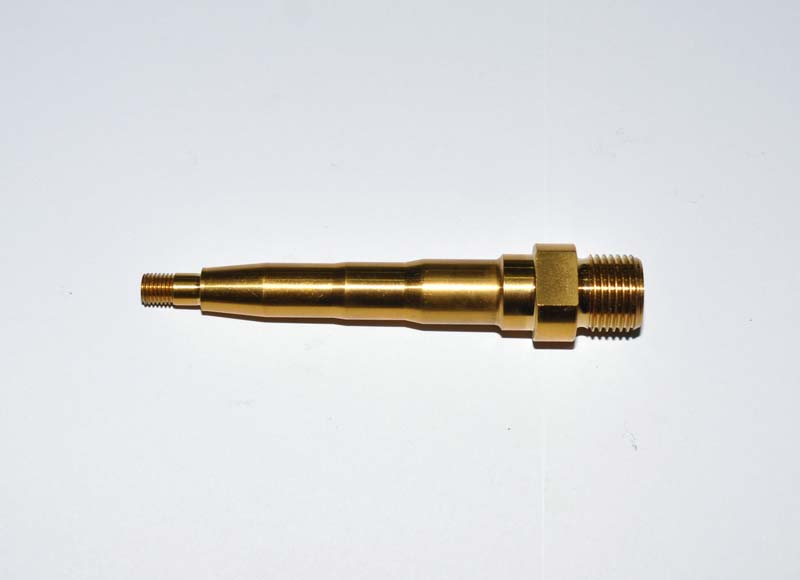
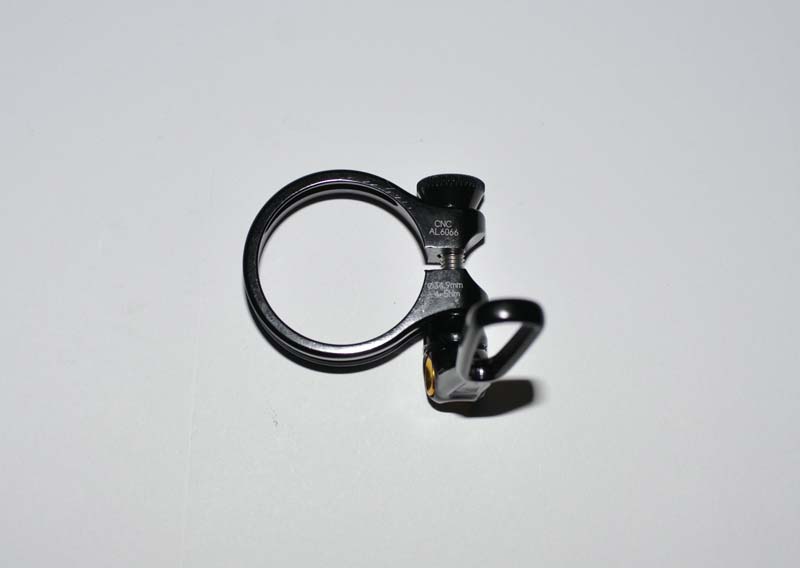
Machined techinicals for the Parts
CNC machining is a good choice for it. CNC machining is a common method for producing bicycle pedals, as it allows for precise machining and faster production times. The machining process should be optimized to minimize material waste and machining time. Our CNC Machined Center is equipped with 3-axis, 4-axis, and 5-axis CNC machining centers, which can be machined simultaneously and ensure precise and tight tolerance to make complex geometries. A smooth, uniform surface finish not only improves the appearance of the part but also can improve its functionality by reducing friction and wear. Oxygenation and mirror polish are chosen for these bicycle accessories. oxygenation and mirror polish could significantly improve the appearance of bicycle accessories. The highly reflective finish creates a bright, shiny surface that is visually appealing and can enhance the overall design of the accessory. Besides, it could reduce friction between moving parts in bicycle accessories.
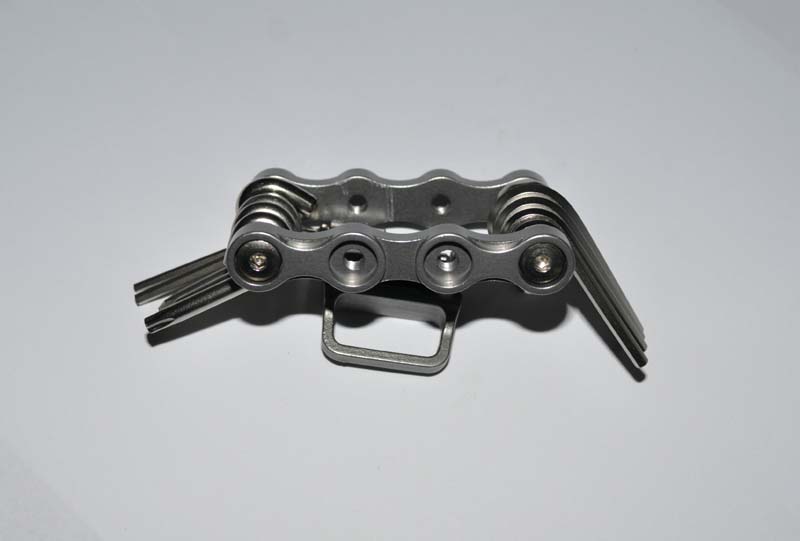
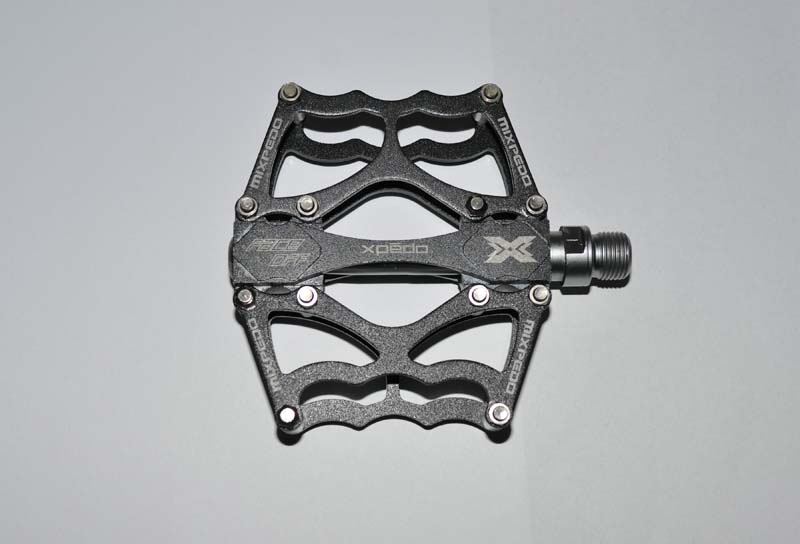
Fast Lead Time
One day, our engineers performed a DFM analysis on the bicycle parts drawings given by the customers, promptly gave effective suggestions to the customers, and formulated a suitable CNC machining process. From prototyping to manufacturing and molding, we carefully inspected the components and packaged them to ensure that they were transported safely during the process. Once the bike parts are delivered intact, the bike exoskeleton components can be assembled immediately, ensuring product delivery to the customer within 7 days. So Sebastian's company persevered, bringing their product to market and testing the market, adjusting their sales plans.
With NOBLE's powerful CNC machining capabilities, Sebastian's bicycle accessories company increased efficiency by 25% and reduced costs, allowing products to be brought to market in a timely manner.
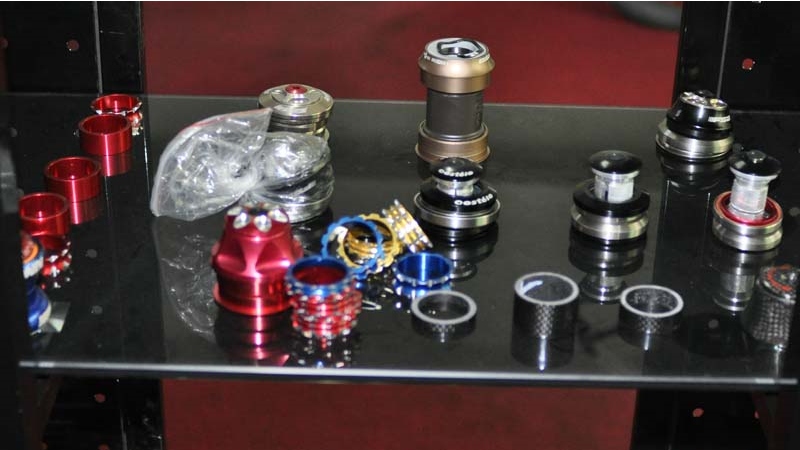
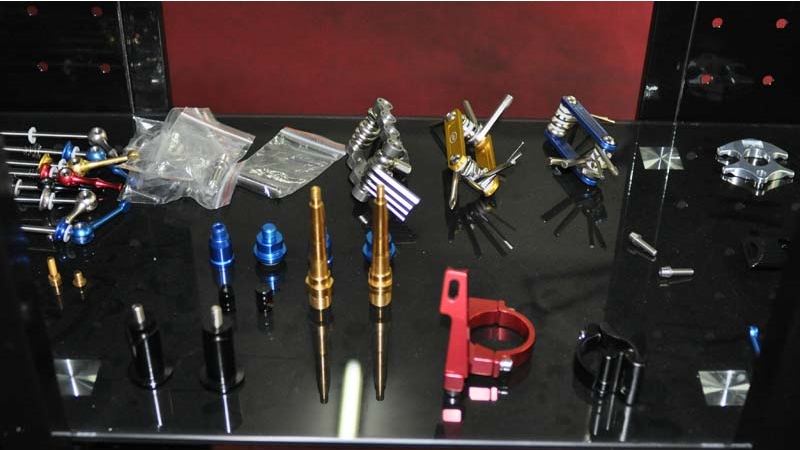
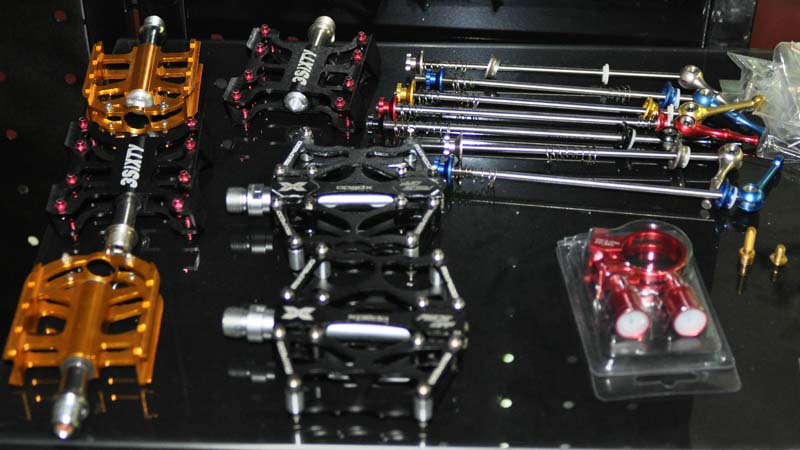