Sheet Metal Stamping Services
Our Sheet Metal Stamping Services
Our sheet metal stamping services manufacture intricate stamping parts accurately and deliver products that surpass customer expectations at an affordable cost and quick turnaround time.
●Tolerance down to 0.001mm
●10+ years experience in stamping
●ISO 9001 & ISO13485 Certified Factory
●Lead Time As Fast As 3 Days
●Advanced Equipment & Competitive Price
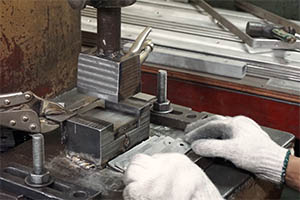
Our Sheet Metal Stamping Capabilities
80+
Machines
±0.001 mm
Tolerances
0PC
MOQ
12+
Surface Finishes
Our Sheet Metal Stamping Process
Our sheet metal stamping services could design and create progressive dies and four-slide tools, as well as precision machining. We are also able to perform any necessary secondary manufacturing processes, such as deburring and tapping. Our team has a deep understanding of metallurgy, and we are committed to providing exceptional customer support for all of our metal stamping and forming products. We can shape and form your workpiece to the optimal geometry and can achieve precision tolerances down to one-thousandth of an inch.
Progressive Die Sheet Metal Stamping
Progressive die stamping is a productive and automated method used for creating high-volume productions. During manufacturing, a strip of sheet metal is fed through a series of dies, each performing a specific operation on the material. This allows for the simultaneous creation of multiple features, reducing production time and cost.
Deep-draw Sheet Metal Stamping
Deep-draw sheet metal stamping is a metal-forming technique that creates seamless, three-dimensional components with significant depth. The process involves using a die and punch set to transform a metal sheet into complex shapes by drawing it into a cavity. This method is commonly used to produce cylindrical or box-shaped parts with high accuracy. Achieving the best results requires expertise in tool and die design, material selection, and process optimization. With the right equipment, skilled operators, and engineering support, deep-draw stamping can produce high-precision, functional components for various applications.
Fourslide Sheet Metal Stamping
Fourslide sheet metal stamping also referred to as multi-slide stamping or four-way stamping, is a specialized method of metal stamping. The manufacturing process is used to create intricate shapes and complex, small to medium-sized components with multiple bends. It is ideal for parts that require precise forming, tight tolerances, and high-speed production. Unlike traditional sheet metal stamping, which uses a single punch and die set, four-slide stamping uses a multi-slide machine. The machine has four horizontal slides, each equipped with different tooling components, including punches, dies, and forming tools. This allows for various operations to be performed simultaneously, making the process versatile and efficient. Fourslide stamping is widely used in industries such as automotive, electronics, telecommunications, medical devices, and consumer goods, where precision and complex geometries.
Fine blanking Sheet Metal Stamping
Fine blanking sheet metal stamping is a precise method of forming metal components that produce smooth edges all the way around the workpiece. Unlike traditional blanking, this method only requires one step and a small die clearance. Furthermore, no additional secondary operations are required, reducing both production time and costs. As a result, fine-blanking is a popular manufacturing technique for a variety of products, including automotive, aircraft, and precision machine components.
Embossing Sheet Metal Stamping
Embossing is a sheet metal stamping technique that produces raised or indented patterns or designs on sheet metal. It entails applying pressure to the material with the desired pattern using a die, resulting in a raised or depressed area. Embossing is frequently used to add decorative or functional features such as grip surfaces or identification marks.
What is sheet Metal Stamping?
Sheet metal stamping is a cold-forming process that uses dies and presses to apply external forces to plates, strips, tubes, and profiles which makes plastic deformation or separation to obtain a workpiece of the desired shape and size. Sheet metal stamping is a low-cost, high-speed manufacturing method that may create numerous, identical metal parts. The sheet metal stamping process can be used to create high-quality products and is appropriate for both short- and long-term production., and can be performed in conjunction with other metal-forming operations to produce high-quality parts.
Advantages of Sheet Metal Stamping
High Efficient
The sheet metal stamping process uses stamping dies and machinery; standard presses can produce a few dozen strokes per minute, whereas high-speed presses can produce hundreds or even thousands. Additionally, a punch may be produced by each stamping stroke.
Thus, sheet metal stamping is effective, simple to use, and amenable to automation and mechanization.
Consistent quality
Through the use of a die, the sheet metal stamping process provides dimensional accuracy and shape consistency, and usually does not degrade the surface quality of the sheet metal stamped parts. The die also has a long lifespan, which ensures stable and consistent quality, and good interchangeability.
More Flexible
Large size ranges, intricate shapes, and workpieces that are challenging to process using other machining techniques can all be processed using sheet metal stamping, such as clocks, automotive longitudinal beams, panels, etc. Additionally, the strength and stiffness of the stamped parts as well as the cold deformation and hardening effect of the sheet metal stamping materials are both quite high.
Low Labor Cost
Sheet metal stamping has features of high material utilization rate, light weight of workpiece, good rigidity, and high strength. Sheet metal stamping generally has no chips, less material consumption, and no other heating equipment. It is a material-saving and energy-saving machining method, which helps to reduce costs.
Sheet Metal Stamping Production Volumes
Our sheet metal stamping services are flexible in various production volume.
Low Volume Production
Customers often utilize small metal stamping orders to bridge the gap between product development and large-scale manufacturing. This allows them to test how their products will perform in the market before committing to larger orders. Additionally, low-volume production can be beneficial for buyers seeking custom products. Even in small batch production, NOBLE is not only of high quality but also offered at a favorable price.
High Volume Production
To remain competitive in today's fast-paced industrial environment, it is critical to meet high-volume production demands while maintaining quality and efficiency. sheet metal stamping is a highly scalable and cost-effective high-volume manufacturing process. Developing custom tooling lowers unit costs.
Long Run Stamping
Long-run sheet metal stamping is a manufacturing process that offers the flexibility to change all factors over time. As a result, production lines can be expanded and optimized to produce high-quality parts with greater flexibility.
Low Cost Production
Sheet metal stamping is more cost-effective than other processes due to lower die and secondary costs and a high level of automation. sheet metal stamping dies are less expensive to manufacture and maintain than other types of dies.
Materials for Sheet Metal Stamping
NOBLE provides a wide range of materials for both our standard and custom metal stampings.
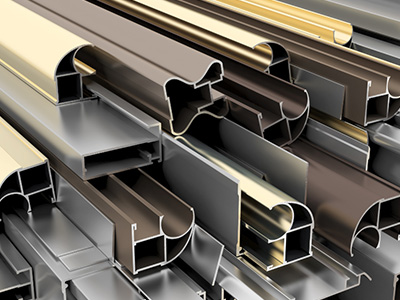
Aluminum
Aluminium is a metal that is lightweight and has good formability, making it ideal for a variety of stamping applications. It is frequently used in the automotive, aerospace, and electronics sectors. For stamping purposes, aluminum alloys like 5052 and 6061 are frequently employed.
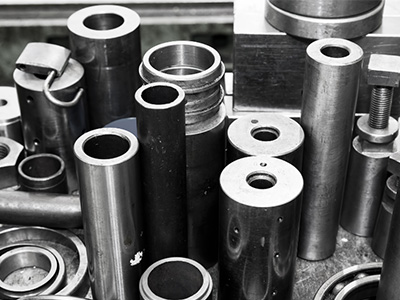
Steel
Steel is the most commonly used material for metal stamping due to its strength, durability, and availability. Various types of steel are used, including carbon steel, stainless steel, and alloy steel. Carbon steel is often used for general-purpose stamping, while stainless steel is preferred for applications requiring corrosion resistance.
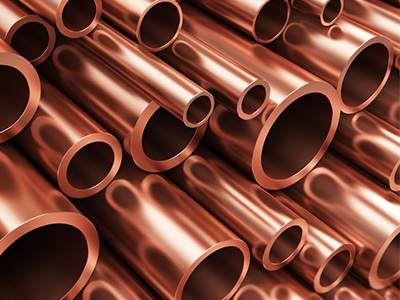
Copper
Copper is renowned for its exceptional electrical and thermal conductivity, making it a popular choice for electrical and electronic components. Copper alloys, such as brass and bronze, are utilized for applications that demand increased strength or protection against corrosion.
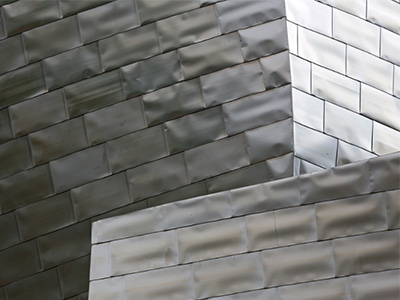
Titanium
Titanium is a lightweight and high-strength metal with excellent corrosion resistance. It is often used in aerospace and medical industries, where its biocompatibility is also advantageous. Titanium alloys, such as Ti-6Al-4V, are commonly used for stamping applications.
Surface Finishes for Sheet Metal Stamping
NOBLE's diverse range of surface finishes can help improve the surface qualities of your products. Surface finishes on your customized parts are intended to improve their appearance, surface hardness, and roughness, chemical and corrosion resistance, and other properties. They also help to hide any visible tool marks from areas cut with live tooling. Here are some of your best alternatives.
Name | Description | Materials | Color | Texture | |
![]() | Anodizing | Anodizing improves corrosion resistance, enhancing wear resistance and hardness, and protecting the metal surface. Widely used in mechanical parts, aircraft, and automobile parts, precision instruments, etc. | Aluminum | Clear, black, grey, red, blue, gold. | Smooth, matte finish |
![]() | Powder Coating | Powder coating is a type of coating that is applied as a free-flowing, dry powder. Unlike conventional liquid paint which is delivered via an evaporating solvent, powder coating is typically applied electrostatically and then cured under heat or with ultraviolet light. | Aluminum, Stainless Steel, Steel | Black, any RAL code or Pantone number | Gloss or semi-gloss |
![]() | Electroplating | Electroplating can be functional, decorative or corrosion-related. Many industries use the process, including the automotive sector, in which chrome-plating of steel automobile parts is common. | Aluminum, steel, Stainless Steel | N/A | Smooth, Glossy finish |
![]() | Polishing | Polishing is the process of creating a smooth and shiny surface, either through physical rubbing of the part or by chemical interference. The process produces a surface with significant specular reflection, but in some materials is able to reduce diffuse reflection. | Aluminum, Brass, Stainless Steel, Steel | N/A | Glossy |
![]() | Brushing | Brushing is a surface treatment process in which abrasive belts are used to draw traces on the surface of a material, usually for aesthetic purposes. | ABS, Aluminum, Brass, Stainless Steel, Steel | N/A | Satin |
Why Choose Us for Custom Sheet Metal Stamping Services
NOBLE prioritizes customer satisfaction by combining cutting-edge technology with the expertise of our skilled professionals. Our Sheet Metal Stamping services are precise, streamlined, cost-effective, and produce excellent results. Choosing our stamping services can help propel your company to new heights of success.
Competitive Pricing
We understand the importance of sticking to your project budget. Our pricing structure is competitive and tailored to meet the needs of businesses of all sizes, whether or not they have limited resources. Our team is available to discuss your budget and provide value-added solutions that are beneficial for your business.
Precision Parts On-Demand Production
If you require metal parts that are of high quality and meet strict specifications, our team can help. We possess extensive knowledge in industry technology, which enables us to offer ultimate design flexibility based on your predefined project criteria.
Strong R&D Support
Our experienced engineers and technicians are available to answer your questions and provide personalized service for jobs large and small to help ensure you get the right part for your needs. In addition to this, an in-house mold shop and dedicated R&D engineers make it easier and more cost-effective to develop new products for customers.
On-Time Production
Large-scale production capacity and professional engineering and sales teams, establish open communication and just-in-time production for your order, which can provide the fastest delivery time to meet urgent needs.
Work with Us in 4 Simple Steps Only
With many years of manufacturing experience, NOBLE offers the best solutions for all rapid prototyping and low-volume manufacturing needs. We streamline the innovation cycle into four simple but effective steps.
Upload Your Design
Just simply upload your CAD filesand submit RFQs with clear infor-mation online.
Receive Design Analysis
We'll send you design for manufa-cturability analysis and transparent pricing.
Start Manufacturing
Our experts will produce your parts with the required technologies and materials.
Receive Your Parts
Your parts will be delivered to your door directly with stringent deadlines.
Gallery of Sheet Metal Stamping Parts
Please browse our extensive gallery showcasing the precision sheet metal stamping parts created by us for our esteemed. clients.clients.
See What Our Customers Say About Us
The feedback of customers has a greater impact than a company's advertising. Take a look at what our satisfied customers have to say about how we met their needs.
Sheet Metal Stamping Applications
Sheet metal stamping is a crucial aspect of parts manufacturing in various industries such as automotive, aerospace, electronics, appliances, telecommunications, and medical equipment. NOBLE is dedicated to offering innovative manufacturing solutions to meet the diverse needs of our clients. Our top priority is to provide high-quality parts at competitive prices to customers across multiple sectors.
Oil & Gas
The professionals at NOBLE have a vast understanding of sheet metal stamping techniques for the oil and gas industry and use top-of-the-line sheet metal stamping machines to guarantee high precision.
Tool & Die
NOBLE's professional engineering team has sheet metal stamping expertise in the tool and die industry, providing you with Professional technical support in tool and mold making, precision machining, material properties, and manufacturing technique selection.
Automotive
Our sheet metal stamping services enables the production of a wide range of components that contribute to the performance, safety, and aesthetics of vehicles in the automotive industry.
Aerospace
Our stamping services provides high-quality, precise, and durable components that meet the demanding requirements of aircraft safety, performance, and reliability.
Medical Devices
Our sheet metal stamping services have been meticulously designed to meet the stringent requirements of the medical industry, ensuring that every component we produce meets or exceeds the highest standards.
Robotics
Our cutting-edge capabilities, innovative craftsmanship, and skilled engineering team could better serve the robotics field with advanced sheet metal stamping solutions.
Sheet Metal Stamping FAQs
- Q
What are the advantages of sheet metal stamping?
ASheet metal stamping offers several advantages, including high production efficiency, consistent part quality, cost-effectiveness for high-volume production, the ability to create complex shapes and features, and compatibility with a wide range of materials. It also allows for automation, which can further enhance productivity.
- Q
What types of products are made using sheet metal stamping?
ASheet metal stamping is used to manufacture a wide range of products across various industries. Common examples include automotive components (such as brackets, panels, and chassis parts), electrical and electronic components, appliances, aerospace parts, hardware, and various metal enclosures.
- Q
What are the key steps involved in the metal stamping process?
AThe metal stamping process typically involves the following steps: design and engineering, material selection, tool and die design, material blanking (cutting), forming (bending, drawing, etc.), secondary operations (such as piercing, threading, or welding), inspection, and finishing.
- Q
What factors should be considered in the design of sheet metal stamped parts?
AWhen designing parts for metal stamping, considerations such as material selection, part geometry, tolerances, draft angles, and bend radiuses are important. Design for manufacturability (DFM) principles should be applied to ensure efficient production and minimize potential issues.
- Q
What kind of operation is sheet metal stamping?
AFlat metal sheets are formed via a manufacturing technique called sheet metal stamping or pressing. A flat sheet of metal—either a blank or a coil—is placed in a sheet metal stamping press during this procedure, where a tool and die surface shape the metal into its desired form.
- Q
What dimension works best for sheet metal stamping?
ASheet Metal, 24-gauge to 20-gauge Brass, copper, and sterling silver are all available in 24-gauge to 20-gauge sheets, which is ideal for sheet metal stamping.
- Q
What restrictions apply to sheet metal stamping?
AYou are usually only able to use relatively low-strength materials, including low-carbon iron or steel, due to the nature of sheet metal stamping processes. The tools frequently break when used with strong materials. By adding ribs and other radii, sheet metal stamped pieces can be made stiffer, but the material must still have some ductility.
- Q
Why is sheet metal stamping beneficial?
ASheet metal stamping decreases the need for several machines, the number of employees, and labor hours, all of which have a substantial negative impact on production costs. As it offers cost reductions compared to other ways, this method is ideal for businesses that require thousands of parts for bulk orders.